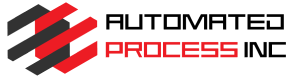
Metal Finishing
Incorporating robotic deburring, grinding, sanding, or polishing into your production process can boost throughput, robotic deburring, specifically, is an automated solution designed to efficiently remove burrs, sharp edges, or fins from metal parts.
Robotic deburring technology enhances both productivity and profitability by enabling continuous operation over extended periods. Robotic systems can be easily integrated into existing projects, with control systems featuring built-in force-control capabilities. This allows for efficient deburring, grinding, sanding, and polishing with minimal effort.
Advantages:
Polishing
Polishing is often a repetitive and tedious task, making it ideal for robots. With robotic polishing, products are polished consistently and precisely in a fraction of the time, with robots applying the perfect amount of pressure and motion. This makes robotic polishing more efficient, reducing cycle times and eliminating the need for breaks.
Robots also reduce the drudgery and safety risks of polishing for workers. They are immune to the fumes and dust typically associated with polishing tasks, and because they use dry abrasive wheels instead of chemical solutions, robotic polishing is more eco-friendly. Robotic polishing saves time, cuts costs, and delivers higher-quality results for the finished product.
Are you excited about innovation and technology? Join our team of experts and partner with a company that is driving the future of industrial automation and robotics.
*By completing this form you're signing up to receive our emails and can unsubscribe at any time